
Ensure your headworks can cope in demanding times
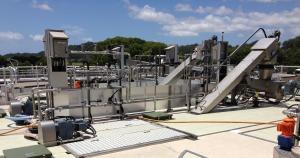
CST's horizontal in-channel rotary drum screening technology is built from the outset, to be robust and adaptable. Screening products that are cheaper up-front just transfer cost and problems down the line.
A successful engineering solution can't be one-size-fits-all. CST’s horizontal in-channel rotary drum screening technology is designed to suit the application.
ROSEVILL, NSW, AUSTRALIA, November 22, 2022 /EINPresswire.com/ -- By Michael Bambridge*Water industry plant operators acknowledge that efficient, robust and easily maintained screening equipment is the most critical stage in municipal and industrial wastewater treatment.
Operators rely on screens to capture the solids that would otherwise flow into the wastewater treatment plant potentially causing damage and blockages to downstream equipment.
This task is growing more demanding, particularly when dealing with unpredictable weather events and ever-tightening statutory license conditions. In North America, regulators are increasingly concerned with water quality, environmental spills and contamination of water tables.
Headworks are the first line of defence in preventing such issues. Wastewater pumps and treatment systems are engineered to handle some impurities, but beyond a certain level, debris and irregular feeds can lead to equipment failures and faster component wear.
The result is higher operating and whole-of-life costs because of the increased downtime. This is in addition to environmental, occupational safety and health risks and clean-up costs.
With local government utilities and smaller industrial plants operating on tight budgets throughout the US, these problems impact their financial resources, hampering their ability to operate and adequately maintain their facilities.
To meet these challenges, CST Wastewater Solutions (CST) have drawn on their experience of over 30 years in wastewater installation and operation, to develop a range of headworks designed for urban wastewater management in industrial applications.
Successful Engineering Approach
A successful engineering solution cannot be based on one-size-fits-all. CST’s horizontal in-channel rotary drum screening technology is thus designed from the outset to suit the application.
Their horizontal in-channel rotary drum screening technology is built from the outset, to be robust and adaptable. Screening products that are cheaper up-front just transfer cost and problems down the line.
As part of this approach, the screens are manufactured locally, allowing better control of production, delivery times and quality. The screens are also operator friendly, accessible and low maintenance. Being manufactured out of stainless steel, they are robust and perform well in harsh and corrosive environments.
CST’s range of screens have validated the company’s engineering approach by delivering proven performance over many years in the Asia-Pacific. These advanced screens are now being introduced to the US water and wastewater industry.
CST’s in-channel technology has lower head loss at peak flows to increase solids removal efficiency compared with traditional screening designs. Their screening technology provides mechanical simplicity, self-cleaning and high-efficiency screening at high flows. This results in reduced maintenance and lower whole-of-life costs compared to band and inclined drum screen designs.
Key to the enhanced performance is the screening drum which is installed horizontally semi-submerged in line with the incoming wastewater. The back plate of the drum re-directs flow radially through the mesh to optimise solids separation and self-cleaning.
The rotary drum is manufactured from either self-cleaning wedge wire for primary screening, or perforated plate for fine pre-membrane bioreactor (pre-MBR) screening. A system of spray nozzles at a moderate pressure provides cleaning of the drum.
An internal hopper collects the screenings, which are flumed out to either the integral lifting and dewatering screw or flumed outside the channel converting high-flow, low-solids sewage to low-low, high-solids, where they are efficiently dewatered and compacted to reduce screenings volume.
The integral lifting screw is shaftless to avoid any blockages even in the presence of fibrous products and includes screen washing. Lifting and screenings handling can also be conducted outside the channel, which increases options for additional washing and dewatering and can be tailored to individual applications.
The horizontal drum design lowers operating depth and range to reduce average screen velocities for higher removal efficiencies and easier cleaning compared to alternative screens.
US market now has access to proven technology
Following their success in Australasia, CST are now reaching out to partners in the US who are interested in expanding their offering with advanced technology that has been widely proven.
Local manufacture delivers the key outcomes of:
• more robust and low-maintenance products
• better whole-of-lifecycle cost
• provide customers ready access to spares
• provide prompt response for customer’s future extensions and retrofits.
*Michael Bambridge BE, ME, is Managing Director of CST Wastewater Solutions. His experience over three decades spans hundreds of municipal and industrial WWTPs throughout Australasia and internationally.
Jack Mallen-Cooper
Whyte Public Relations
whytepr@whytepr.com.au

Distribution channels: Agriculture, Farming & Forestry Industry, Energy Industry, Environment, Food & Beverage Industry, Waste Management
Legal Disclaimer:
EIN Presswire provides this news content "as is" without warranty of any kind. We do not accept any responsibility or liability for the accuracy, content, images, videos, licenses, completeness, legality, or reliability of the information contained in this article. If you have any complaints or copyright issues related to this article, kindly contact the author above.
Submit your press release